In a previous post (Why no door envelope testing when passive certification is bypassed?) I questioned the lack of a quality control process on my passive build when I chose to bypass certification. I won't bore the Group with the year-long hassle I had to go through to get my doors installed (mostly) correctly. But to demonstrate to other homeowners why a quality control process is a necessity, I'm including "before" and "after" thermal images of the problem areas in the three Zola doors in question, at the bottom of this post.
For prospective passive house buyers I have this advice:
- Before signing any build contracts go directly to the door and window manufacturer's representative (you DO know who that is, right?) and begin a relationship. Your door and window package is way too expensive, and too important, to leave this to others.
- Have the rep walk you through the quality control process required to properly install and verify the performance of their products in your particular house. In my case, I naively assumed all of this was somehow "automatically" put in place for me by the builder. It was not.
- Confirm with the rep that both the builder, and any installers the builder intends to use, have the experience and skills to carry out their parts of the quality control process. If the rep can't lock that down for you, or doesn't have experience with each of the actors involved, consider it a red flag. You may have to force a change in the roster, coach.
- Make sure you find out when specialist skills provided by the manufacturer are required, and just how that interaction is managed. And find out how quickly that specialist skill can be available at your job site. You're going to need it. I certainly did.
- Get the manufacturer's Warranty in your hand and have them mark out which parts apply to your specific build, and which do not. I naively assumed that the Warranty would have to be at least as good as that for high quality windows used in non-passive construction. My mistake.
- If there are parts of the Warranty that leave holes in your coverage (perhaps your build site is within a mile of Puget Sound?) this is the time to either (a) have the manufacturer modify the Warranty for your build in writing, or (b) accept the Warranty as is and the risks that go along with it, or (c) talk to other manufacturers.
- Get a copy of the Sales Contract form to go along with the Warranty. Your agreement with manufacturer consists of both, and they interact. I never received either document until I was having on going problems getting my installation fixed, and that was a year after my build started. And then only after I demanded them. That is way too late, homeowner!
For current passive homeowners I have this advice. If your builder didn't provide you documentation that your building envelope and doors and windows were tested and corrected as needed, they probably were not. After all, your builder has a clear financial incentive not to perform quality control. If your builder intended to produce a quality product, they will have a documented process of quality control, have executed it, and be proud to prove the level of quality achieved on your build. If you don't know the quality of what was delivered to you, I would suggest you test it and find out.
Prospective and current passive homeowners can take the conversation offline with me (
cavendum.e...@gmail.com) if they want more details, or just to find out how I used thermal imaging to perform my own quality testing.
C
*****
Entry door "before" thermal image (below). The vertical
purple area is an air leak from the door handle to the floor where the
door is out of adjustment. The purple blob at the lower right is an air
leak under the door assembly where it wasn't sealed properly by the builder.
Entry door "after" thermal image (below). The
vertical leak was fixed by the Zola tech door adjustment. The leak at
the lower right was blocked with sealant applied by the Zola tech.
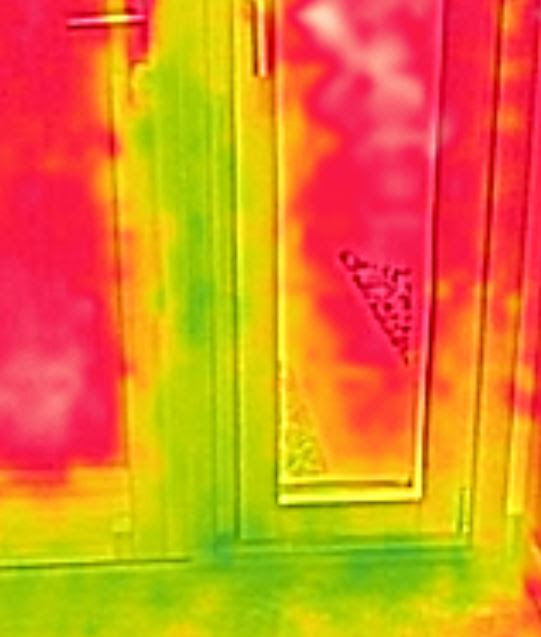
Side door "before" thermal image (below). The
vertical purple area is an air leak from the central door hinge down to
the floor; the door is out of adjustment. The dark blue areas at the
bottom left and right of the door are air leaks were caused by damage done to the door
sill, and door seals, by the builder and subcontractors using the door without protecting the sill.
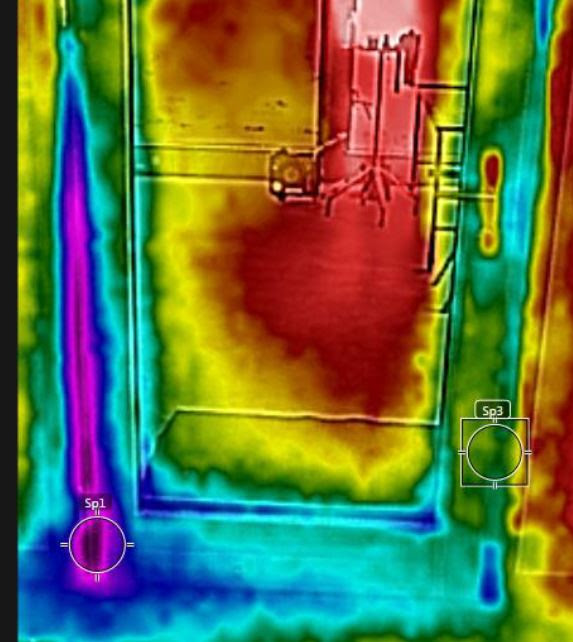
Side door "after" thermal image (below). The
vertical leak was fixed (almost completely) by the Zola tech door
adjustment. The leaks along the bottom were stopped with new seals
applied to the door sill and the door itself. Because of the damage done to the sill, and the bottom of the door, those parts could
only be partially repaired without replacing the entire sill assembly.
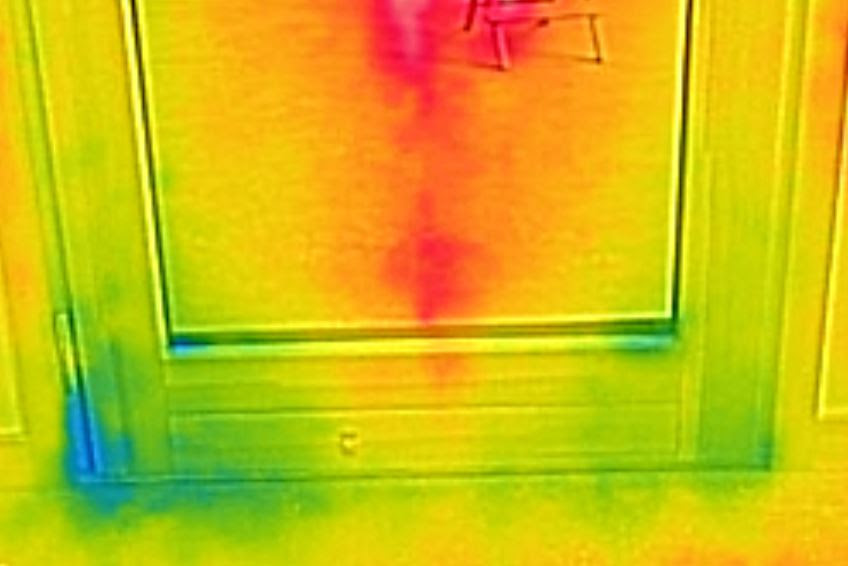
Slider door "before" thermal image (below). The
horizontal purple and blue area is an air leak caused by parts missing from the
door installation. The area of the hole in the seal was about the size
of a golf ball... you could feel air blowing in from the outside. The
installer didn't verify that the door seals were properly installed (or missing entirely in this case).

Slider door "after" thermal image (below). The same area with seal installed. After I proved the leak to the builder, the manufacturer forwarded a replacement seal.
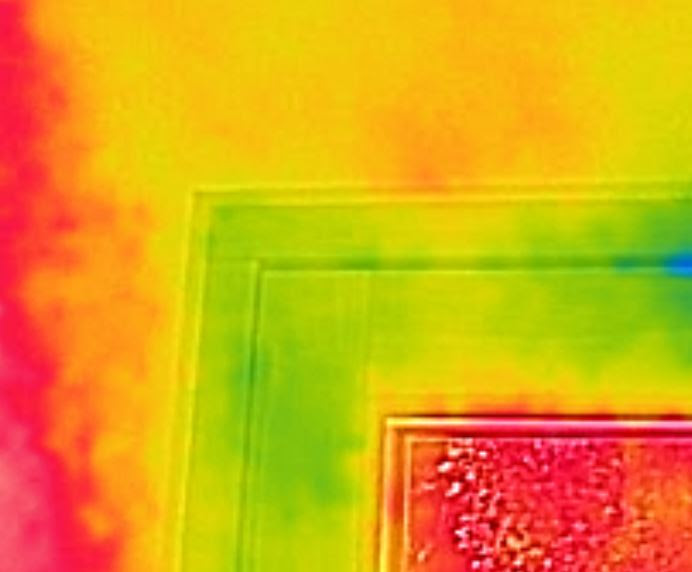